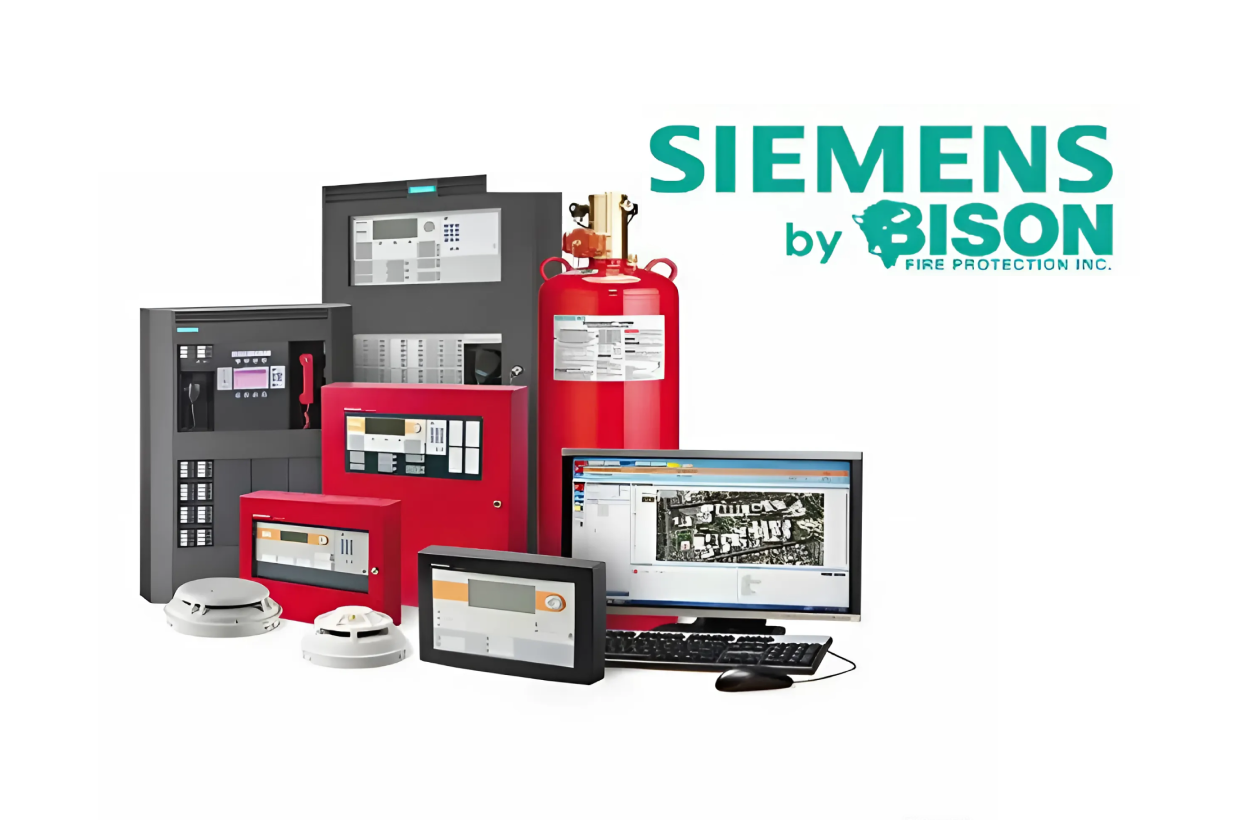
Are Top Tier Fire Alarm Systems Really More Expensive?
With rising costs on every front, these days’ people are always looking for areas to save a few $$$. Even in life safety. High-quality fire alarm systems, such as Siemens, while initially appear more expensive, they are less costly in the long run compared to low-quality systems due to several